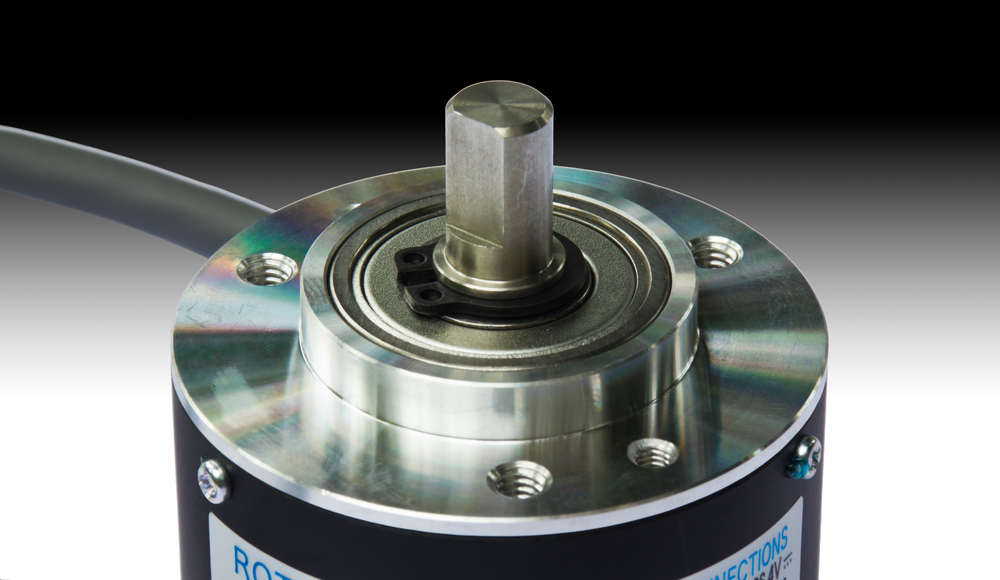
If you run any industrial application that uses motion control or motion feedback, you should know that an encoder is crucial to your production.
These nifty units play a vital role in production finding applications for a myriad of industrial devices, including:
- Robotics
- Conveyor
- Plotting
- Counting
- Labeling
Often, these devices need to operate quickly and with a high accuracy level.
What Does an Encoder Do?
The encoder is the device that provides the positioning feedback to the system.
Essentially, an encoder works by converting motion into an electric signal. This signal is then transmitted to a control device to serve its intended purpose.
Encoders produce electric signals from different types of technologies, including magnetic, optical, resistive, and conductive mechanical technologies. The most common types of signal generation technologies are optical and magnetic.
Optical encoders produce a signal from the interruption, or lack thereof, of a light hitting a photosensitive plate. While optical encoders are quite effective, they are also quite sensitive to dust and must, therefore, be protected properly in any plant.
Magnetic encoders convert changes in magnetic flux into an electric signal. They contain a set of north and south poles. As the object being measured passes across those poles, the sensor reads the changes in the magnetic field.
Types of Encoders
There are two main types of encoders – rotary encoders and linear encoders.
Rotary Encoders
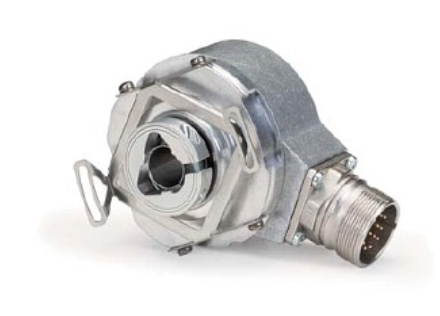
Rotary encoders, also known as shaft encoders, are used to sense and transduce rotation angles. These are the most common types of encoders. Most of the time, when people talk about encoders, they are usually referring to rotary encoders. It converts angular position or rotation angle into an electric signal. The signal can be analog or digital, depending on your needs.
As the name suggests, rotary encoders are motor-driven. Further, rotary encoders are classified into absolute rotary encoders and incremental encoders.
Absolute encoders are used to show the position of the motor’s shaft and are used to show angular displacement. On the other hand, an incremental encoder generates a signal that provides motion-related information, which is then processed to determine position, speed, and distance.
Linear Encoders
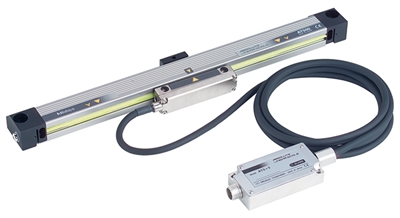
Linear encoders or linear scales are used to measure an object’s linear movement. They detect distance, direction, speed, and linear displacement. A linear encoder contains three main components – a scale, a signal source, and a receiver.
Like rotary encoders, linear encoders are further categorized into absolute and incremental linear encoders. Absolute encoders are used in applications that require information about a specific and accurate displacement like in elevators, milling machines, and linear actuators. Incremental actuators, on the other hand, are used in devices that perform simple operations where angular displacement specificity is not crucial. Such devices include grinding machines, jig borers, and stepper motors.
ACS Industrial Services Can Help with a Faulty Encoder
Encoders are used in a diverse array of fields, which often involve high temperatures, dusty conditions, oily and moist conditions, vibrations, and shock. These factors, coupled with normal wear and tear, can cause your encoder to start malfunctioning. It might start to give an incorrect output or no output at all.
The good news is that often, encoder issues can be repaired relatively inexpensively.
Our technicians at ACS Industrial Services use the latest diagnostic technologies to repair and test standards for a wide array of encoders. Whether your unit is faulty or for scheduled maintenance, we can help. With our Rush Repair Service, you can get your encoder unit back in 2-5 days. We also guarantee our repairs with a 2 -year warranty.
To learn more about encoder repairs, contact us via our website or call us directly at 800-605-6419.