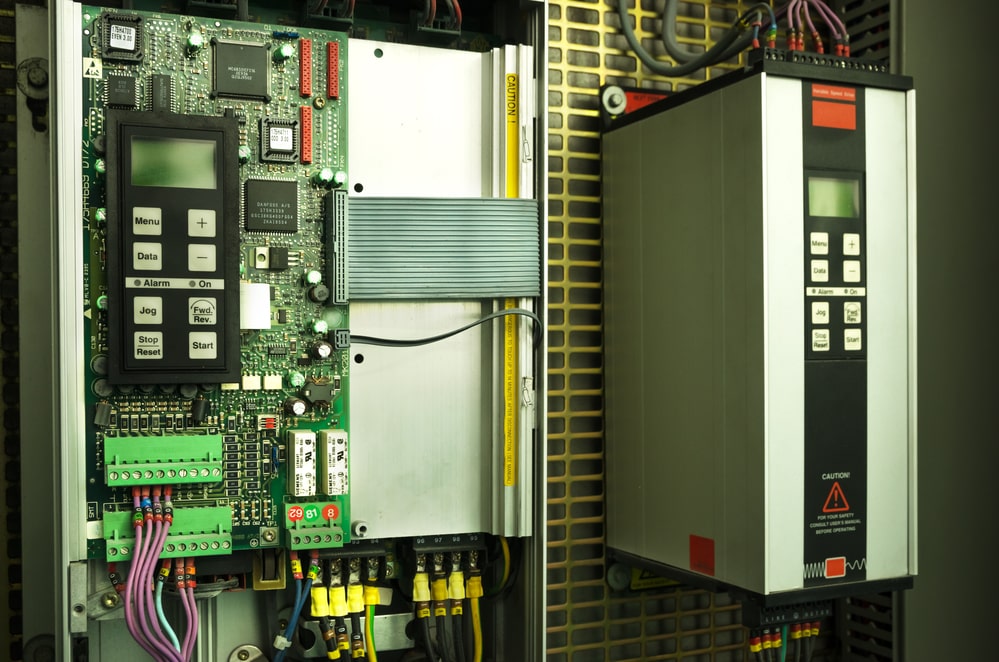
Electric motors are used in a myriad of engineering fields, and in most cases, the speed and torque of each motor should match the process’ desired parameters. Since this cannot happen naturally – the speed or torque can be too high or too low – an inverter is added into the system between the electrical supply and the motor.
It’s recommended to match the motor’s speed or torque to the required specifications since this increases the system’s overall efficiency, thus reducing wasted energy.
What Is an Inverter Drive?
An inverter drive converts DC voltage into AC voltage with the help of an intelligent power module, which is also commonly referred to as an IPM. The IPM is a network of power transistors. Additionally, inverters are used to control the speed or torque of electric motors.
Inverter drives are also referred to as AC drives, Variable Frequency Drives (VFD), or Variable Speed Drives (VSD). As mentioned above, VFDs are set up between the motor and the power supply. This allows them to receive the power from the electrical supply and regulate its voltage and frequency accordingly before it reaches the motor.
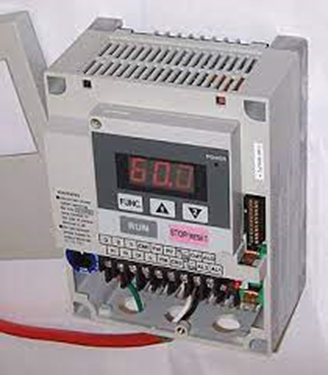
How Does an Inverter Work?
To understand how an inverter works, it’s best to first delve into its construction. An inverter drive comprises three main units, a rectifier unit, a DC intermediate circuit, and an inverse conversion circuit.
Rectifier unit
The rectifier unit converts AC voltage from the power supply into DC voltage. In most cases, the rectifier unit comprises at least 6 rectifiers – two for each phase in a three-phase system. One of the rectifiers only allows negative voltage through while the other only allows positive voltage through, resulting in DC voltage.
DC intermediate circuit
Through its inductors, the DC intermediate circuit smoothens the DC voltage generated by the rectifier unit. This unit also contains capacitors to store after receiving it from the rectifier.
Inverse conversion unit
This is the unit responsible for converting DC voltage back into AC.
Benefits of an Inverter Drive
Inverter drives benefit many motored systems. Below are some of the benefits you can gain by using an inverter.
Saving energy
Inverters can reduce energy consumption by anywhere between 20 to 50% by controlling the power supplied to the motor. This is especially true for fans and pumps.
Soft starting
Inverters control the speed of a motor by controlling the frequency of the voltage supplied to the motor. This phenomenon is utilized by engineers to control the acceleration and deceleration of systems that should not have load dropouts, such as elevators and conveyor belts.
Reversing the motor
Inverter drives only require a small amount of current to change a motor’s direction of rotation.
Stabilizing the power line
Starting an AC motor requires a tremendous amount of power. They often can cause a huge drain in the power distribution line, which might cause some equipment such as sensors to trip whenever such a motor starts.

Do You Need Help With a Damaged Industrial Inverter Drive? ACS Industrial Services Can Help
Inverters can develop problems that could halt production. Some of the most common issues are overvoltage, undervoltage, and overcurrent.
ACS Industrial has experience with most inverter drive brands. If you run into an issue with your inverter drive that’s out of warranty, reach out to us via our website or call us at 800-605-6419 to speak to a member of our customer support team.