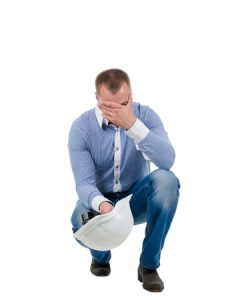
Are you suffering from an expensive case of downtime – the unplanned kind? Unplanned downtime in manufacturing is a budget-killer like no other. Some estimates put the average cost at $7,900 per MINUTE and its rising! It’s frustrating to watch production come to a stop and deliveries go unmet. Finger-pointing is a waste of time, so let’s get to it.
If you want to identify and prevent machine failures resulting in downtime you need to be willing to look in all directions including, possibly, at yourself. Why? Because industrial catastrophes are rarely caused by a single person or event. According to the NTSB, typically between 12-14 events have to coincide before a failure actually occurs.
Start here: Identify the Cause:
Unless an unavoidable single incident occurs (such as a meteor lands on your plant), you have many potential causes of failure – both human and physical – and usually some of both. Here are some to consider
- Physical Damage
- Corrosion
- Fatigue
- Overload
- Wear
- Environmental – water, heat, humidity, lightning, electrical imbalances, etc.
- Human Error
- Inadequate Maintenance/Maintenance Errors
- Operational Error
- Design Errors
- Installation Errors
- Failed or non-existent cyber security
- Untrained/under-trained personnel
And that’s just the short-list, but it’s a place to start. Speaking of starting …here are 5 ways to start dealing with that expensive downtime.
5 Ways to Start Eliminating Downtime
- Track your downtime – This is THE most important part because you can’t fix them if you don’t even know what the problems ARE. If you are not already doing this, it’s time. There are plenty of helpful off-the-shelf programs and automatic trackers (or experts if you want outside help) to zero in on the problems. This will alert you in real time as the problems happen. Record these and then periodically analyze the data so you know exactly where to focus your efforts.
- Invest in Proper Training/Hire the Right People/Skills – Human error is a BIG problem. These can stem from the front end at poor machine design and installation, to operator error, all the way to just plain ignoring the warning signals of impending machine failure for way too long. Proper training costs far less in the long run than damage, downtime, and unexpected repairs.
- Set up a Regular Maintenance Program and Stick to it – There are plenty of approaches to this depending on the type and size of your plant and the type of equipment and manufacturing software you use. CMMS (computerized maintenance management systems) is a HUGE subject and sites such as Reliable Plant and Plant Services.com are a helpful place to start. It is too important to ignore.
- Practice Preventive Maintenance & Repair Equipment – Not replacing worn parts, misalignments, bad connections, improper storage, corrosion, bad bearings, machine overload, lubrication issues – the list is endless – are all frequent causes of production disruption and potentially expensive repairs or worse, replacements. Keep your employees in the loop on this effort, make your priorities clear to all, and encourage (and reward them) for finding ways to keep things running or increase productivity. Have a go-to industrial electronic repair center that meets your needs.
- Protect Your Assets – Facility, Equipment, People – Invest in the best you can afford whether its cyber security, safety equipment and training, humidity and temperature controls, power backup systems, or primary power conditioning for electrical load balancing. It all matters and is part of the success equation to eliminate costly, unplanned downtime.
Preventing unplanned downtime is a HUGE subject in manufacturing, and for good reason as it is the biggest cause of lost production. There is far more to the subject than I can cover here, but there is plenty of information to be found on this subject and plenty of very helpful consultants.
About the Author: ACS Industrial Services is an independent industrial electronic repair center providing repairs for all types of industrial electronic equipment and most all manufacturers including power supply repairs, circuit board repairs, drives, servo motors, CNC equipment, encoders, monitors and touchscreens, test equipment, and much more. Rush Service is available and Two Year Warranties cover most repairs. Our helpful customer service team members are available to answer your questions and help solve your industrial electronic repair problems. You can reach them by calling 800-605-6419 or going to www.acsindustrial.com.