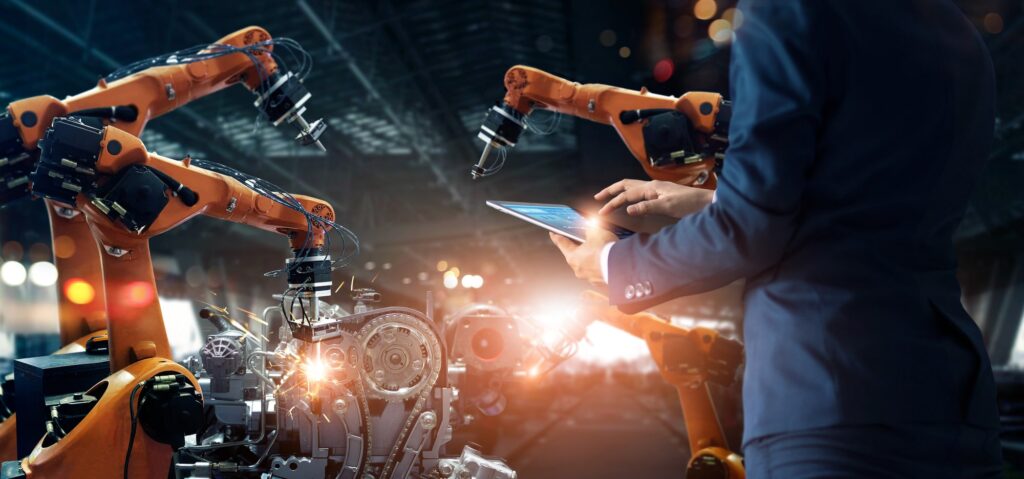
The relentless march of industrial automation has placed robots at the heart of manufacturing processes. These tireless machines have transformed production lines, but their continued operation hinges on effective maintenance. Traditionally, industrial robot maintenance relied on a reactive approach – fixing breakdowns as they occurred. However, this reactive strategy caused costly downtime and disrupted production schedules.
To address these limitations, a new era of proactive, data-driven maintenance strategies has emerged, promising to revolutionize the way we keep robots operational.
The Cornerstones of Modern Maintenance
The cornerstone of modern industrial robot maintenance lies in its predictive nature. Proactive maintenance leverages the power of prognostic algorithms, which analyze sensor data collected from robots in real-time. These algorithms can identify subtle changes in operational parameters that might signal an impending component failure. By anticipating these failures, technicians can schedule maintenance interventions before breakdowns occur, minimizing downtime and maximizing robot availability.
Sensor networks play a critical role in predictive maintenance by weaving a web of data around robots. Embedded within the robots themselves, these sensors continuously monitor factors like vibration, temperature, and energy consumption. The collected data is then fed into the prognostic algorithms, enabling them to detect anomalies and predict potential issues.
Another cornerstone of modern maintenance is the concept of digital twins. A digital twin is a virtual replica of a physical robot, containing a comprehensive set of data that mirrors the robot’s real-world state. This digital counterpart allows technicians to virtually troubleshoot potential problems, test maintenance procedures, and optimize robot performance without disrupting actual operations. Digital twins can be used to train new technicians in a safe and controlled virtual environment.
Emerging Technologies on the Horizon
The future of industrial robot maintenance promises to be even more transformative with the integration of emerging technologies. Augmented reality (AR) has the potential to revolutionize how technicians maintain robots. AR overlays digital information onto the real world, allowing technicians to see critical data projected directly onto the robot they are working on. This can streamline complex maintenance procedures by providing technicians with step-by-step instructions and real-time visualizations of internal components.
Collaborative robots, or cobots, are another exciting development poised to reshape the landscape of robot maintenance. These robots are designed to work safely alongside human technicians, assisting with tasks and sharing the workload. Cobots can be programmed to handle repetitive or hazardous tasks, freeing up human technicians to focus on more complex maintenance activities. This collaborative approach can not only enhance efficiency but also promote skill transfer, as human technicians learn from their robotic counterparts.
Final Thoughts
The future of industrial robot maintenance promises to be exciting for business owners and maintenance professionals alike. Predictive algorithms, sensor networks, and digital twins will provide the foundation for proactive maintenance strategies. Meanwhile, augmented reality and cobots will further enhance technician capabilities and streamline maintenance workflows. By embracing these innovations, industries can ensure their robots remain operational and productive, driving a new era of efficiency and growth.
Let ACS Help with All Your Industrial Robotics Maintenance Needs
Navigating the intricacies of robotics maintenance can be challenging, but you don’t have to do it alone. At ACS Industrial Services, we specialize in ensuring your robotics systems equipment remains in operation. See our Robotics Repair Service page for more information.
With over 20 years of experience, ACS is a leading industrial circuit board repair service provider. We repair single- and double-sided circuit boards across various makes and models. We provide a rapid turnaround time. Most repairs are back in your hands within 7-15 days, with our Rush Repair Service typically shipping in just 3-5 days.
When you choose us, you can expect real people, honest work, and accurate results. We showcase the dirty, gritty work + magic that gets electronics back up and running. Contact us for a FREE evaluation and a no-obligation quote, or call (800) 605-6419.