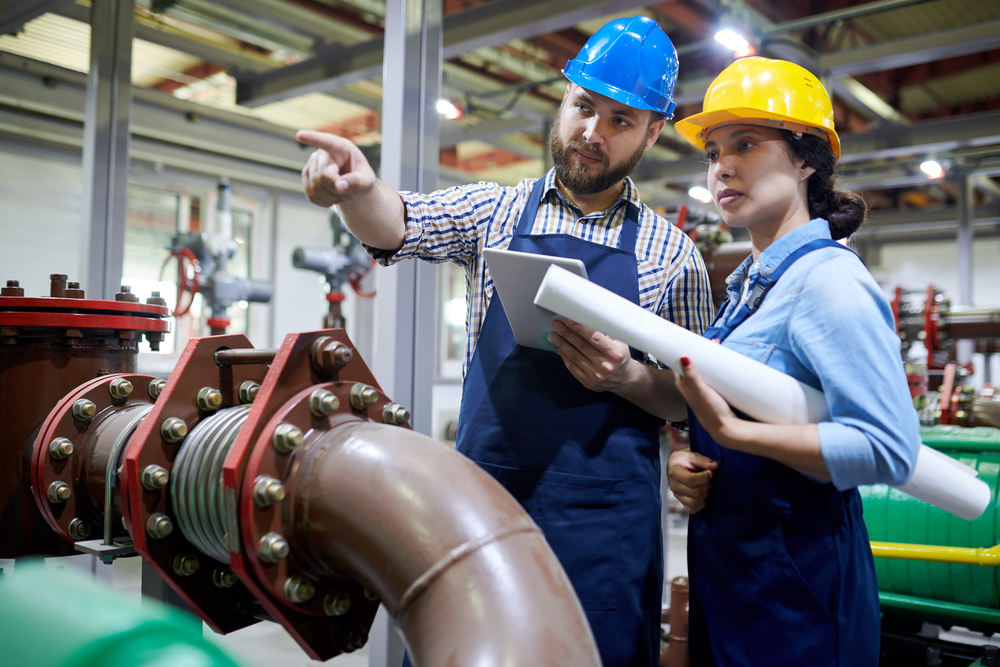
To ensure machines’ longevity, optimum efficiency, and safety of employees, any company that manages physical assets needs an efficient preventative maintenance program. One such program is reliability-centered maintenance, commonly referred to as RCM.
RCM was first implemented in the aviation sector. However, many other industries worldwide adopted and continue to adopt RCM in their assets integrity management program. It is foundationally analytical, meaning companies can replicate it successfully in any field.
What Is Reliability Centered Maintenance?
RCM is a maintenance program that helps to identify potential failures in a machine, the consequences of those failures, how asset managers can prevent them, and what to do when failure is inevitable.
Reliability-centered maintenance was first documented by F.S. Nowlan and H.F. Heap in a report published by the U.S. Department of Defense in 1978. In the report, Nowlan and Heap defined RCM as “a scheduled-maintenance program designed to realize the inherent reliability capabilities of the equipment.”
Constituents of a Reliability Centered Maintenance Program
Over the years, since its first implementation, many other parties have come up with maintenance systems called RCM despite being different from the traditional RCM. This necessitated a standard that gave birth to the technical specification SAE-JA1011.
This technical standard does not explicitly describe a singular process. Instead, it outlines the minimum criteria a maintenance process must meet to qualify as reliability-centered maintenance.
It asks seven questions that create a roadmap to identification, prevention, and response to a machine’s functional failures. Below is a discussion of the seven questions.
1. What is the asset supposed to do, and what are its associated performance standards?
This question helps to identify the equipment’s intended functions. When answering this question, it is best to provide specific metrics in describing an equipment’s functions. For example, ‘To provide 300 gallons of water per minute”.
2. In what ways can the equipment fail to perform its intended functions?
The second part helps to describe the ways that the equipment might fail to perform the intended functions. For example, “Provides less than 300 gallons of water per minute”.
3. What are the potential causes of failure?
Function failures can arise from various factors, including equipment fatigue, human error, design flaw, and less than ideal operating conditions.
4. What are the effects of each failure?
This question answers how each potential failure may affect the quality, rate, and cost of production.
5. How does each function failure matter?
This question extrapolates the broader risks that could arise if a piece of equipment fails. Steps 4 and 5 help to validate the required maintenance practices.
6. What systematic processes should be applied to reduce the probability of failure?
By highlighting the consequences of each failure in steps 4 and 5, asset managers can prioritize the order in which they need to mitigate each failure. Selecting a maintenance task over another should be based on each failure’s magnitude of consequences, occurrence probability, and mitigation costs.
7. What should be done if failure is inevitable?
This question addresses what should be done if you cannot find a suitable prevention task for any failure identified in the earlier steps.
If that kind of failure occurs at the end of the equipment’s life cycle, it’s best to plan and schedule a replacement of the entire equipment. However, if it happens early in the life cycle, teams should redesign or modify the parts causing the failure.
Contact ACS Industrial Services. We are Here to Help!
After years of frustration from a lack of reliable electronic repair services, we started ACS Industrial Services to solve industrial repair problems quickly, cost-effectively, and with friendly service.
Call us today at 800-605-6419 or use the contact form on our website to speak to a team member.