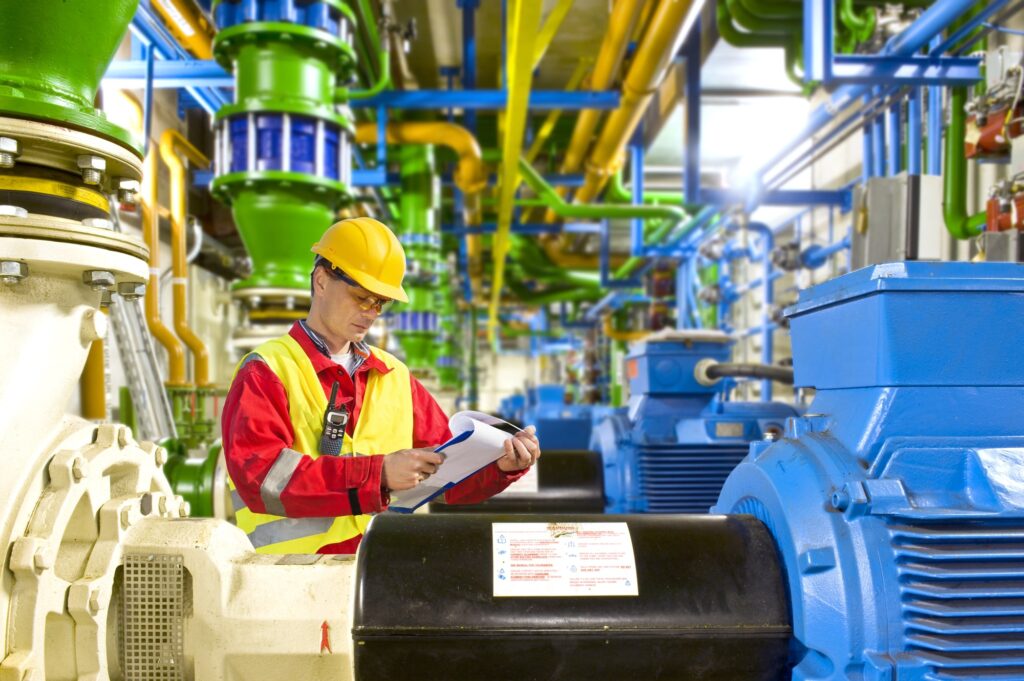
In today’s factories, industrial electronics are like the heart and brains of the operation. But how these important systems are taken care of can really affect how well a factory works, how long its machines last, and how much money it makes. A recent survey by Plant Services found some surprising things: only 27% of factories plan a yearly shutdown for maintenance, 18% never stop at all, and 35% don’t know what to do with the information they get from their machines, and some even doubt if it’s correct. This shows a worrying trend in how maintenance is done today.
Reactive Maintenance: The Expensive “Break-Fix” Model
Reactive maintenance, also called the “break-fix” model, is the old way of doing things. You only fix something when it breaks. This seems simple, but it costs a lot. When machines unexpectedly stop working, production gets delayed, deadlines are missed, and customers get unhappy. Emergency repairs often mean paying extra for parts and paying workers overtime.
There’s more to it than just money. Reactive maintenance can cause a chain reaction of problems. One broken part can cause other connected parts to fail, making repairs even more expensive. Constantly fixing things in a rush wears out machines faster, so they need to be replaced sooner.
Preventive Maintenance: A Smart Investment
Preventive maintenance (PM) is a different way. It means checking, cleaning, fixing, and replacing parts on a schedule, before they break. It’s like taking your electronics to the doctor for regular checkups to find problems early. This may seem like an extra cost, but it’s a smart move that saves money in the long run.
PM stops surprise breakdowns, which means less downtime and fewer losses. It also lets you plan maintenance better, saving on labor costs. Regular upkeep helps find worn-out parts before they cause trouble, saving other parts from damage.
Preventive maintenance isn’t just about saving money, it’s about making everything run smoother. Well-maintained machines work better, so products are better and more consistent. It also makes the workplace safer by reducing the chance of big accidents.
Real-World Challenges & High-Tech Solutions
The benefits of preventive maintenance are clear, but it’s not always easy to do. The survey shows that many factories struggle to understand and use the information they get from their machines. But new technology is changing how maintenance works.
Sophisticated sensors and monitoring systems can now gather lots of real-time information about how machines are doing, how they’re performing, and what’s happening around them. This information can be studied with computer programs to find potential problems before they get worse.
By using predictive maintenance, a type of PM, factories can plan their maintenance better, focusing on the areas that need it most. This means maintenance is not just on time, but also targeted, making the most of resources and minimizing disruptions.
Let ACS Help with All Your Preventative Maintenance Needs
Knowing how to keep your equipment running can be tough, but you don’t have to do it alone. At ACS Industrial Services, we specialize in preventative maintenance services for industrial equipment.
With over 20 years of experience, ACS is a leading industrial repair service provider when things break. We repair many different components of machinery across various makes and models. We provide a rapid turnaround time. Most repairs are back in your hands within 7-15 days, with our Rush Repair Service typically shipping in just 3-5 days.
When you choose us, you can expect real people, honest work, and accurate results. We showcase the dirty, gritty work aka magic that gets electronics back up and running. Contact us for a FREE evaluation and a no-obligation quote, or call (800) 605-6419.