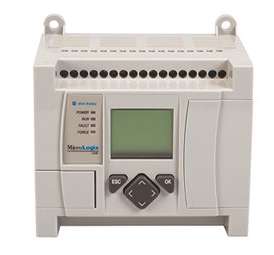
Let’s say one of your PLCs is faulting or behaving erratically affecting your manufacturing production. Besides being frustrated, you also now face some tough choices knowing that your primary objective is to keep production going and to minimize downtime.
PLC system troubleshooting can get complicated so we are going to stick to the basics here and focus on the PLC itself. The processor often gets blamed for PLC problems but in fact, the majority of PLC faults occur with an I/O card.
Before going any further, you should remember two things. Protect yourself and your investments by:
- Always keeping a PLC program backup(!!) and keeping it protected from heat, humidity, and EMI/RFI damage
- Shutting down your PLC and the main power before changing modules or putting your fingers or tools in any electronic equipment
Some of the things that can cause your PLC to behave erratically, or not work at all, include:
- The main power is off – yes, this is obvious, but rule out the obvious first
- EMI – electromagnetic interference and RFI – radio frequency interference. Nearby arc welding, lightning strikes, radio transmitters with powerful RF, and even large motors starting up nearby can cause disruption to PLCs and other electronic equipment if they are not protected properly. Power conditioning, grounding, and shielding are the solutions to these problems.
- Faults in a field circuit – if this happens, disconnect wiring at the module and field device and check for a short circuit
- Bad power supply – find the source of power to your PLC and check to see if there is any output from the power supply as this is a frequent cause of PLC failure; if there is no power output, replace the power supply module and you should be back in business.
- Overheating – look for error codes and/or visual signs of overheating such as discoloration
- Bad I/O channels
- Bad back-up batteries (This tip comes with a WARNING: Change these batteries regularly before they die; if the red battery light comes on do NOT down the power and change the batteries until you get your program backed up or you will LOSE your program.)
- Power fluctuations or surges
- Bad cables/loose cable connection
- Machine age
- Temperature extremes and excessive humidity
More helpful tips on PLC troubleshooting:
- Check the sensor inputs to the PLC
- Identify output controlled by input on PLC ladder diagram
- Ensure that output LED is cycling on/off with output
- Make sure field circuits are fuse protected; if not, the PLC processor can be destroyed by a short circuit or over-current condition
- Reset the PLC using the reset key switch if you have one; check the manual to make sure this will not interrupt your program or other sub-set programs
- Consider getting a cellular modem and SCADA system if you don’t already have them to receive PLC alarms and to remotely control your PLCs.
- Keep a current ladder diagram, wiring diagram, and manufacturer’s manual for each of your PLCs where you can find it easily – you will be glad you did. The manual can guide you in the specifics of troubleshooting your particular PLC.
- Does it matter if your PLC is digital or analog when troubleshooting? Not really. Basic troubleshooting is very similar for both types of units.
Sometimes you just can’t figure it out or don’t have the time or expertise to troubleshoot a PLC. This is precisely the situation our tire manufacturing customer found themselves in recently when they sent us their Allen Bradley PLC MicroLogix 1100. It was alarming and behaving erratically. Our techs got it repaired and shipped back out to the customer in three days so it could go right into tire production…for less than half the cost of purchasing a new one.
If your PLC unit is having problems and is still under warranty, contact your OEM. If it is out of warranty it is still repairable by an experienced industrial electronics repair house. They should offer free evaluations, accurate quotes and a warranty on both their parts and labor. They should also offer rush service for when you are really under the gun on time.
ACS Industrial Services is an independent expert industrial electronics repair service with facilities in Maryland and North Carolina. In addition to servicing PLCs, ACS Industrial also provides drive repairs, power supply repairs, circuit board repairs, servo motor and encoder repairs, touch screen and CRT monitor repairs, test equipment repairs, and much more.