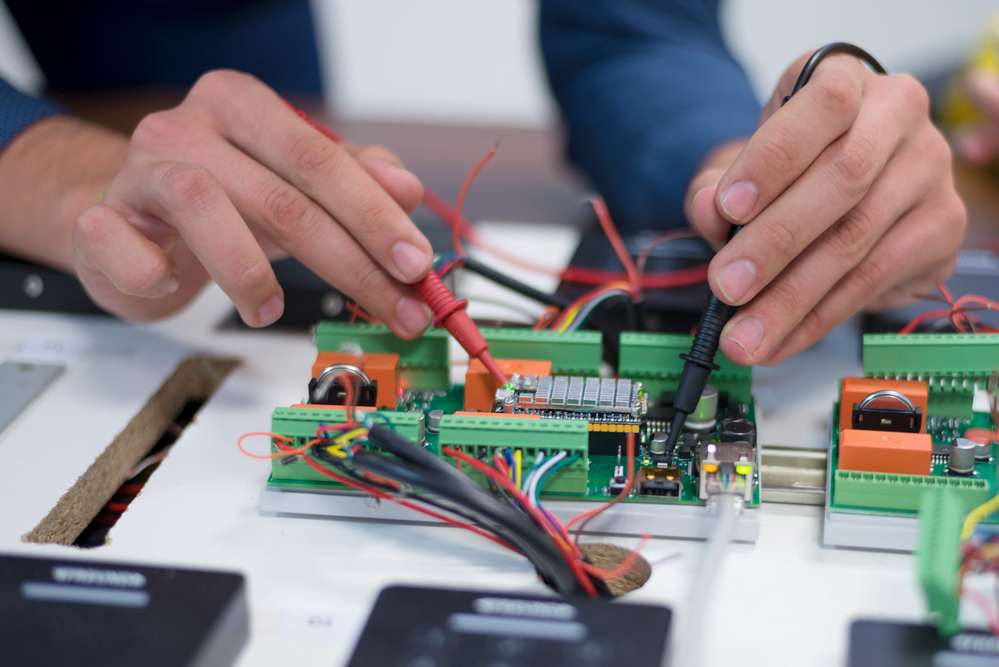
When your critical machinery fails, it can feel like your whole operation comes to a halt. But what really happens after you ship off that malfunctioning drive, faulty power supply, or damaged circuit board to an industrial repair shop? Today, we’re giving you a behind-the-scenes look into the industrial electronics diagnostics and repair process, so you know exactly what to expect from start to finish.
Step 1: Equipment Arrival & Initial Evaluation
Once your equipment arrives at the repair facility, it’s not just thrown onto a workbench. Every item undergoes an initial visual inspection and logging process. Serial numbers are recorded, symptoms noted, and it’s carefully assessed for visible signs of damage like burnt components, corrosion, broken connectors, and even shipping damage. This stage sets the foundation for in-depth industrial electronics diagnostics.
Step 2: Initial Evaluation and Diagnostics
Next, each unit undergoes an initial evaluation by our skilled technicians. During this free evaluation, our team inspects the equipment for obvious physical damage, common known issues specific to that device, and any indications of previous repair attempts. Technicians will test suspected components to assess basic functionality and identify any clear signs of catastrophic failure, which could indicate that the unit might be beyond repair.
It’s important to note that our free evaluation does not include detailed, component-level diagnostics—that level of testing is available through our paid evaluation service. Many customers appreciate our transparent approach, with free evaluations helping them understand the overall condition of their equipment and enabling accurate repair pricing based on visible and testable damage.
Step 3: Component-Level Repair & Circuit Board Restoration
Once the problems are diagnosed, repairs begin at the component level. This isn’t a swap-and-replace job—technicians restore functionality by replacing only the defective components with high-quality parts that meet or exceed OEM specs.
In cases where boards suffer from physical damage or corrosion—common in water-damaged or overheated units—the repair team performs circuit board restoration. This may include cleaning, solder rework, and repairing or replacing damaged traces.
Step 4: Retesting & Quality Assurance
Once repairs are complete, the unit isn’t just packed up and shipped out. It undergoes thorough functional testing, often in simulated real-world conditions. For servo motors, that means dynamic load testing; for VFDs, full-power ramp-ups. Circuit boards are tested in working systems or on custom test benches to ensure all signals and voltages are within spec.
This step ensures that every repaired item performs just like it did when new—if not better.
Step 5: Packing & Return to Service
After passing quality assurance, the equipment is carefully cleaned, labeled, and securely packed for return shipping.
When your equipment returns, it’s ready to be reinstalled and go back to work—minimizing downtime and saving you the high cost of buying new.
Why Industrial Electronics Diagnostics Matter
Understanding the complete repair process not only builds trust—it shows how much value can be recovered from even heavily damaged gear. With accurate diagnostics, targeted repairs, and professional-grade circuit board restoration, your “broken” equipment still has plenty of life left in it.
Call ACS Industrial for Repairs and Service for Your Industrial Electronics!
Knowing how to keep industrial electronics in operation can be tough, but you don’t have to do it alone. At ACS Industrial Services, we specialize in preventative maintenance and repair services for industrial electronic equipment.
With over 20 years of experience, ACS is a leading industrial repair service provider when things break. We repair many different components of machinery across various makes and models. We provide a rapid turnaround time. Most repairs are back in your hands within 7-15 business days, with our Rush Repair Service typically shipping in just 3-5 business days.
Contact us for a FREE evaluation and a no-obligation quote, or call (800) 605-6419.