Encoder tips to diagnose problems… BEFORE sending out for encoder repair service.
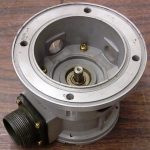
If motion control is important to your production, then your encoder is one of the keys to your success. Encoders are exposed to shock, contaminants/oil, excess vibration, moisture, and high temperatures that regularly put their toughness to the test.
There’s a lot of encoders out there in industry, doing their job 24/7. These little workhorses include: incremental aka quadrature encoders which uses a transparent disk with section equally spaced to determine movement; absolute encoders which use a photodetector and LED light source and a disk with concentric circle patterns; linear encoders which use a transducer or reading-head linked to a scale; magnetic rotary encoders which use hall effect sensors; and commutation encoders which are similar to incremental encoders but have commutation tracks along the outer edge of the disk.
First, start out right! Two basic rules apply to buying encoders:
- Buy the best you can afford – Yes, this seems obvious – encoders are no place to show off your frugal nature. If you can afford it, make sure you buy the latest and greatest encoders. These have built-in diagnostics systems that monitor the device’s functioning and let you know when maintenance is needed before it becomes a production disaster.
- Choose the Right Encoder– Encoders are highly reliable and accurate, relatively low cost and can be incorporated into many different existing applications from packaging machines to robotics to CNC machines. That’s the good news. The bad news is that encoders can be easily damaged by excess vibration, dirt, oil, dust, moisture and other contaminants. Optical encoders are sensitive to direct light source interference. Magnetic encoders can be damaged or affected by magnetic or radio interference as well as bearing failures, seal failures and disk shattering. Incremental encoders often suffer count loss. So know your needs and choose accordingly.
Other considerations when choosing the right encoder include:
- Index Channel – Power failures common in your plant? Index channel will be useful.
- Desired Resolution (CPR) – CPR are cycles per revolution; key to the number of output pulses per complete revolution. Your industrial sales rep can help with this.
- Noise and Cable Length – The longer the cable length the more noise. Use shielded twisted-pair cables with low capacitance value.
- Cover/Base –Covers and base or mounting options can be especially useful for work environments with excess moisture or vibration.
- Output – Depends on the application’s requirements and which type of encoder you have
Ok. So you’ve bought the best you can afford and, for some reason, your encoder is now not performing well, or at all. Now what? Here’s a few troubleshooting tips.
Encoder Troubleshooting Tips:
1.Incorrect Output – Getting the wrong or distorted output? Random faults? This can be caused by several things including: loose wiring, electrical noise, bad alignment, or incompatibility with driver or controller. Check the connections and alignment of the encoder and the shaft.
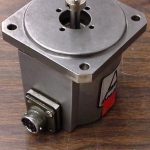
2. No output – If your encoder appears “dead” with no movement, it may be severely damaged but there are a few other things you can check before sending it in for encoder repair service: check for loose connections, incorrect voltage supply, in correct signal type, loose connections. If you have a qualified technician you can swap the encoder for another to see if the encoder is the problem. If the encoder is the problem, don’t panic. Most encoders are easily repairable.
3. Worn-out Ball Bearings- How to tell: Entire drive unit becomes irregular as the frequency inverter tries to compensate for the loss of several pulses. This is usually due to normal age/wear or poor installation of the bearings resulting in premature wear.
4. Dirt/Dust Contamination – How to tell: The encoder produces one pulse too few or does not rotate. Why? Dust particles on the incremental disc fools the rotary encoder into detecting two increment lines as just one. Use an encoder with an external plug connection to help avoid this. You may also need a cover.
5. Moisture Contamination – How to tell: Sporadic failures. Moisture may have gotten in through the cable gland.
6. Overheating/Heat Damage – How to tell: Usually total failure. Hot exhaust air from the motor fan passes over the encoder causing it to overheat.
You already know your encoder is vital for your production. They allow you total control over speed, direction, and distance. Choose right, buy the best and practice good maintenance of both your equipment AND your shop environment to keep yours running smoothly.
Even if you’ve done your due diligence, eventually even the best maintained encoders will likely suffer damage, age or contamination and fail. The good news is that most encoder problems are economically repairable by an experienced industrial electronics repair center.
About the Author: ACS Industrial Services is an independent industrial electronic repair center providing repairs for all types of industrial electronic equipment and most all manufacturers including power supplies, circuit board repairs, drives, servo motors, CNC equipment, encoder repairs for BEI, Heidenhain, Dynapar, Allen Bradley, Fanuc, Sumtak, Tamagawa, Yaskawa, Fincor, and many others, monitors and touchscreens, test equipment, and much more. Rush Service is available and Two Year Warranties cover most repairs. Our helpful customer service team members are available to answer your questions and help solve your industrial electronic repair problems. You can reach them by calling 800-605-6419 or going to www.acsindustrial.com.