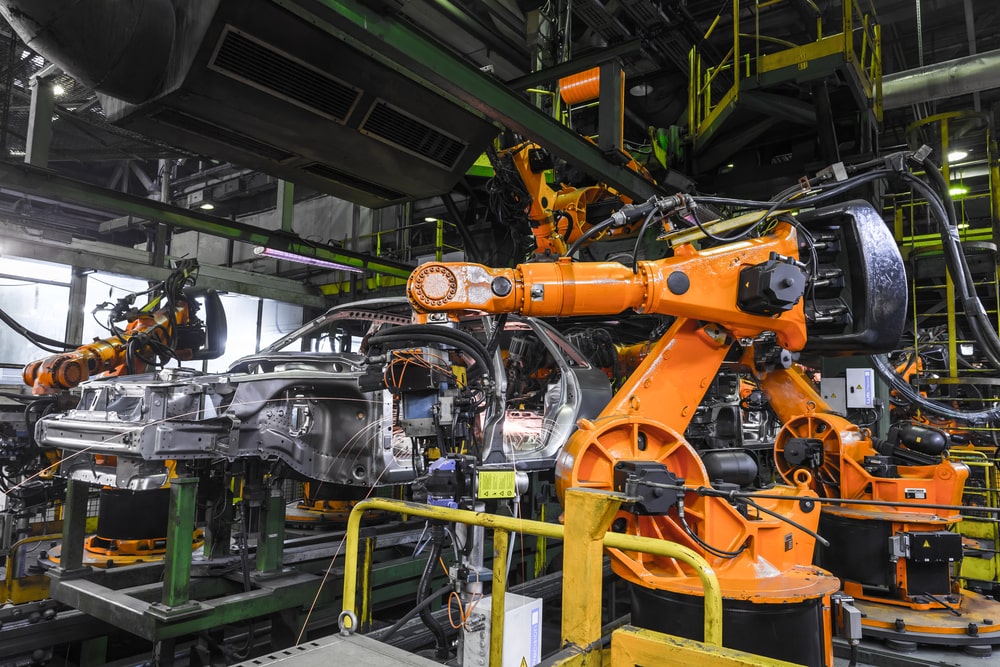
Fanuc servo motors are essential in industrial machinery, especially in CNC machines, robotics, and automated systems. They provide precise and reliable motion control, which is critical for efficient operations. When these motors malfunction, it can lead to downtime, slower production, and high costs. Choosing the right service provider for repairs ensures your motors stay in good working condition, reducing disruptions and extending their lifespan.
Signs Your Fanuc Servo Motor Needs Repairs
Recognizing problems early can save time and money. Common signs of a failing servo motor include strange vibrations, unusual noises, overheating, or inconsistent performance. If your machine shows error codes related to the motor, this could also indicate a problem. Ignoring these issues might cause the motor to fail entirely, leading to longer downtimes and more expensive repairs. Acting quickly can help avoid these risks.
Problems with Choosing the Wrong Repair Provider
Not all repair services are the same. Selecting an inexperienced or uncertified provider can lead to incomplete or poor-quality repairs. A poorly repaired servo motor might work temporarily but fail again soon after. Worse, improper repairs can cause more damage to the motor or connected systems, making the problem even more costly to fix. Taking the time to choose a reliable service provider is essential to avoid these pitfalls.
What to Look for in a Repair Service
When selecting a service provider, prioritize those with expertise in Fanuc servo motors. Look for technicians with specialized training and certifications, as this shows they have the knowledge to handle the unique needs of these motors. A reliable repair shop should also have diagnostic tools to identify and fix the root cause of the issue, not just treat the symptoms.
Additionally, the provider should use genuine Fanuc replacement parts. Authentic parts maintain the performance and durability of the original motor, while low-quality or counterfeit parts can lead to more problems. Providers who offer warranties on their repairs show confidence in their work and provide extra assurance for their customers.
Considering Turnaround Time and Costs
Minimizing downtime is a top priority in industrial settings. Ask for an estimated repair time to understand how quickly your motor can be returned to service. While fast service is important, it shouldn’t come at the expense of quality. Transparency in pricing is also critical. A trustworthy provider will give a clear estimate with no hidden fees. Comparing quotes from multiple providers can help you find a balance between quality and affordability.
Additional Services to Look For
Some repair providers offer extra services that add value, such as maintenance programs or on-site support. Regular maintenance can identify potential issues early, saving you money and preventing unexpected breakdowns. On-site support is especially helpful for businesses with complex systems that can’t afford to lose time transporting motors to and from repair shops.
Keeping Fanuc Servo Motors Running Smoothly
After repairs, regular care and maintenance are key to keeping your servo motor in good condition. Create a schedule for cleaning, lubrication, and inspections to catch any potential issues before they become major problems. Monitor the motor’s performance and address minor concerns promptly. A good repair provider can also help with periodic check-ups to ensure optimal performance.
Key Takeaways
- Fanuc servo motors are critical for industrial operations, and keeping them in good working condition is essential.
- Choosing the right repair service provider reduces downtime, ensures high-quality repairs, and helps your equipment last longer.
- Look for experienced technicians, use of genuine parts, transparent pricing, and additional support options.
- Taking these steps ensures your motors stay reliable, helping your operations run smoothly and efficiently.
Call ACS Industrial for Help with Your Fanuc Servo Motor Repairs!
Knowing how to keep servo motors up and running can be tough, but you don’t have to do it alone. At ACS Industrial Services, we specialize in preventative maintenance and repair services for industrial equipment.
With over 20 years of experience, ACS is a leading industrial repair service provider when things break. We repair many different components of machinery across various makes and models. We provide a rapid turnaround time. Most repairs are back in your hands within 7-15 business days, with our Rush Repair Service typically shipping in just 3-5 business days. Contact us for a FREE evaluation and a no-obligation quote, or call (800) 605-6419.