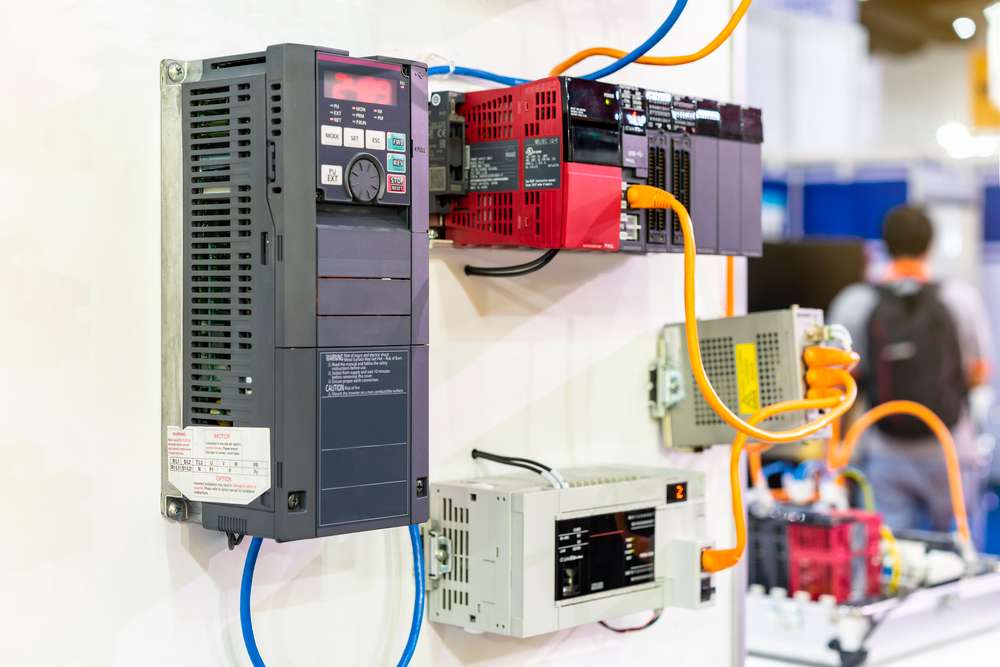
Are you getting over voltage faults from your VFD? Erratic operation? Hearing strange noises? VFD failure? Chances are you may need to change your use and maintenance routines for your VFD and probably other equipment too. As a rule, VFDs are reliable as hell. But like most things, they have their critical needs, and sadly, their breaking points.
A variable frequency drive (VFD) controls the speed, torque, and direction of an AC motor. It is also referred to as an AC drive or inverter. This sounds pretty basic, but the electronic guts of the operation are actually complicated and need consistent maintenance by qualified operators.
We’ve produced a helpful bullet list of common causes of VFD failures, along with maintenance and repair tips. If there’s ONE takeaway, it’s this – avoid what we call the “Electronic Axis of Evil” like the very costly plague it could become: dirt, heat, and moisture.
Top Reasons for VFD Failure and Tips to Identify and Prevent Costly Problems:
1) Buildup
Mainly this means “gunk” made up of dust combined with typical plant air which usually contains oil, moisture, and metallic particles. This buildup is probably the number one cause of VFD failure! And it’s not the actual dirt itself. It’s that the dirt/dust buildup attracts moisture and prevents good airflow. This results in excess heat, and the metallic particles can create stray current paths on your circuit boards. A triple play by the bad guys! The result? At a minimum, you will get diminished performance from your drive and at worst, catastrophic failure – bang!
Prevention tips:
- Clean regularly – everything. And have a solid maintenance schedule so cleaning doesn’t get overlooked. You can regularly spray air through the heat sink and fan, and compressed air in the VFD. Avoid spraying contaminated plant air by using a dedicated air supply that is non-static generating (you don’t want to add electro static discharge problems.)
- Use the correct VFD for your plant environment. Some have side vents for cooling airflow but these can be more prone to dust contamination. Other drives are in a sealed, dust-free housing.
2) Excess Heat
Excess heat is usually caused by buildup, as discussed above. But excess heat can also be caused when the current exceeds the drives rated level and/or by loose connections. You can check the connections visually but it may require a temperature probe or handheld digital pyrometer. The connections should never be hotter than the connecting wires. It’s also recommended to check the temps of the drive and motor.
Overheating can result in blown capacitors and other components. It can also cause shorts which may not be enough to blow a fuse or trip an overload but just enough to shut down the controller and have you wondering why production came to a stand-still. Here’s how to prevent this problem:
- Use a temperature probe to check on the connections, the drive and the motor to make sure they meet the OEM’s requirements.
- Maintain a clean, well ventilated environment
- Regularly check the fans for any sign of bearing failure or foreign objects. This is usually a noisy problem and easy to track down.
- Look for bulging or leaking capacitors. Having either of these means you should shut down the drive immediately and get it repaired! The risk is an expensive cascade of component damage.
3) Moisture/Condensation
Moisture or condensation are common problems in many plants. Excess moisture can cause corrosion, damaging the circuit boards in your electronics. A VFD that operates 24/7 usually creates enough heat from the heatsink to prevent internal condensation. If you run yours less often, you will need to take steps to prevent condensation. What can you do about this?
- Dehumidifiers can help but make sure they are not dripping near electronic equipment. There are many dehumidifier choices so get help making the best choice for your environment.
- If you operate a food processing facility, you need to call in the experts on this subject.
- Choose a VFD with a sealed housing if possible.
- Regularly fire up any stored backup VFDs to make sure they are operating at peak performance and store them in a clean, dry, protected area. Having a VFD down and no decent backup will cost you in multiple ways.
4) Loose Connections/Component Damage
If you are having erratic performance from your VFD, loose connections and bad/aging components are likely causes. Vibration and heat cycles are typical causes of loose connections, which can then lead to dangerous arcing. Arcing at the output can damage other components and cause overcurrent faults. What can you do?
- As a part of your PM cycle, regularly inspect the components looking for bulging or leaking capacitors, date codes on the capacitors (caps need to be replaced after about 5-10 years), damaged fans, problematic heat sinks, corrosion and/or damaged traces on circuit boards.
- Take voltage measurements preferably with the VFD in operation. The OEM will have measurement guidelines for this. Voltage problems can indicate bad capacitors, a bad diode bridge, and/or transistor leakage. You can check for voltage drop across the connection if you are powered up or resistance through a connection if you are powered down. Isolate the connection to get a reliable reading.
- Do not just automatically “re-torque” screws as a way of checking the tightness which can result in more harm than good. Check your manual as this often requires an infra-red check with a digital pyrometer.
- Do not exceed the operating limit. This means getting the proper training and/or familiarizing yourself with the OEM’s recommendations.
- Do not connect the input power to the output motor terminals. This actually happens and it can destroy the power module and possibly cause catastrophic damage. Not all VFDs are set up the same way so check carefully.
- Re-educate yourself if you buy a VFD from a different manufacturer than what you are used to. Don’t assume the operation or maintenance is the same. The OEM’s maintenance guidelines do vary.
5) Using the Wrong Motor or Machine
Connecting your VFD to an incompatible motor can cause it to degrade in performance over time. While this degradation might not manifest immediately, it is more likely than not to cause issues down the line. Additionally, if the machine connected exceeds the drive’s limits it might cause the VFD to heat up. How to prevent this:
- It is best to always refer back to your owner’s manual to confirm the compatibility of the motor or machine that you are looking to control. Some machines work well with a soft starter instead of a VFD.
- When you’re unsure of the right machine to connect your VFD to, talk to an experienced VFD technician for help.
6) High Bus Fault
This is a common fault in VFDs. It is normally caused by external factors such as when there is an instantaneous spike in the AC line voltage or when the machine’s inertia creates an overhauling load. This load continues to rotate faster than the motor’s recommended speed, causing the VFD to take protective measures. You can tell when a high bus fault occurs because the VFD will trip and shut off the insulated gate bipolar transistors. What can you do about this?
- Ensure that your plant’s AC power supply is consistent.
- You should also adjust the deceleration time to match the load’s capability. However, if your plant’s processes require to decelerate rapidly, you may use dynamic breaking or add a regenerative power control circuit.
Still have questions or concerns about your VFD? Do you think it may need service? If it’s still under warranty, contact your OEM. If it is out of warranty, contact an independent industrial electronic repair center. They should offer free evaluations for your VFD and, if needed, a free quote for repairs. They should also provide repair reports and a good warranty that covers both parts and labor.
About the Author: ACS Industrial Services is an independent industrial electronic repair center providing repair services for drives of all types and most all manufacturers including VF drive repairs, servo motors, encoders, printed circuit boards, monitors and touchscreens, PLCs, test equipment, and much more. Our customer service team is available to answer your questions and help solve your industrial electronic repair concerns. Rush Service is available. You can reach them by calling 800-605-6419.