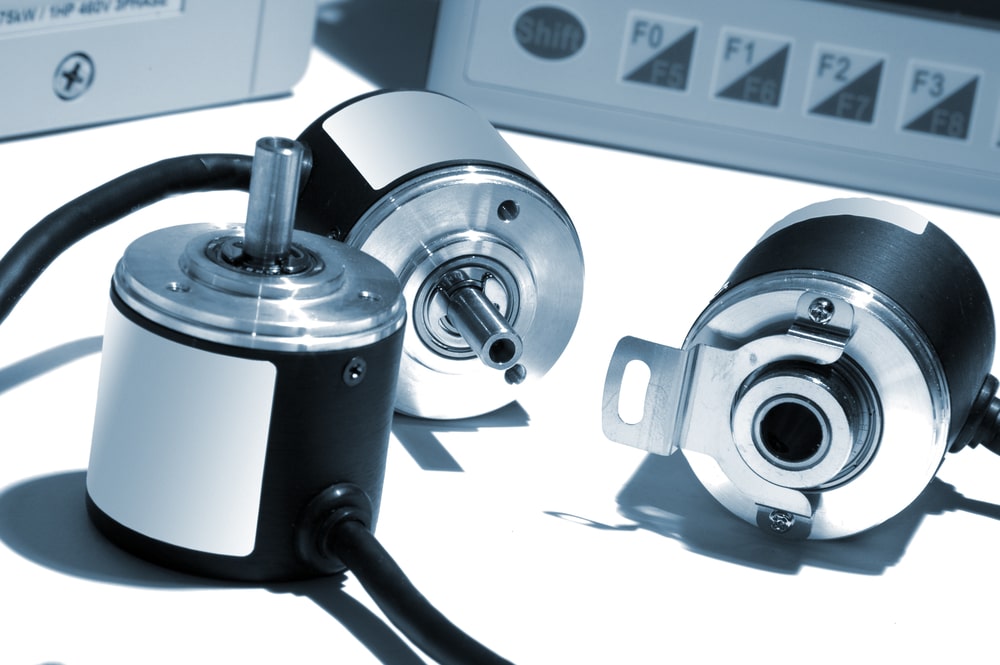
Choosing the right motor is critical for the efficiency and productivity of your industrial applications. When picking between servo and stepper, it can be difficult as there are many factors to consider, including torque, speed, efficiency, cost, and more. When properly applied, both stepper and servo motors can deliver effective and dependable power for a highly successful system.
What Is a Servo Motor?
A servo motor is a motor controlled with feedback. It is a closed-loop motor linked to an encoder that controls positioning and provides speed feedback. This feedback helps to control its motion. If the motor is not in the right position, the controller sends a signal to the motor to proceed until it reaches the desired position.
What Is a Stepper Motor?
A stepper motor is a brushless DC motor that is designed to provide a certain number of defined steps per revolution. Its coils are arranged in phases, making it easy to move in discrete steps. The powering of each phase happens in sequence; thus, the motor rotates one step per phase.
What Is the Differences Between Servo Motor and Stepper Motor?
It is vital to first understand what distinguishes these motors and their advantages and disadvantages. Let’s explore the key fundamentals and how they affect their performance:
Motor Design
Servo motors and stepper motors have different pole counts. Servo motors have a low pole count of between 4 and 12, while stepper motors have a higher pole count of above 50. The motion seems to be continuous because of the high pole count, and the motor moves in a closed-loop system. On the other hand, servo motors require an encoder to regulate pulses, which makes the system more mechanically intricate, leading to further regular maintenance and higher costs.
Stop Accuracy
Both motors can stop accurately. For a stepper motor, this feature depends on the manufacturing quality of the mechanical and electrical windings. On the other hand, factors such as assembly accuracy, encoder resolution, and algorithm facilitate a servo motor’s stop accuracy.
High Speed Performance
Servo motors have higher speed performance than stepper motors as the former usually outputs more torque at a definite RPM than a stepper motor.
This variance in rotation performance is due to the difference in pole count. A stepper motor’s high starting speed helps move the load from a rest position, which is vital for start/stop applications.
The high pole count of stepper motors allows them to produce high torque and run smoothly at low speed. The low pole count of servo motors does not generate high starting torque but maintain constant speed throughout its entire speed range. Therefore, servo motors can offer high-speed torque.
Efficiency
Stepper motors only operate on full current, while servo motors draw only the required current for the motion profile and the load. Since the current is proportional to temperature, this results in increased service life and lower power consumption for the servo motor. The stepper motor however fails to offer this kind of efficient current control as it requires more feedback, which would mean closing the loop.
Learn More from ACS Industrial Services
Do you think your servo motor needs repair? The good news is you can get expert help from an experienced industrial electronics repair center. For all of your industrial electronic repairs, contact ACS Industrial Services. Use our RMA Form link or Contact Us to get a free evaluation. You can also call us at 800-605-6419 to speak with a member of our customer care staff.