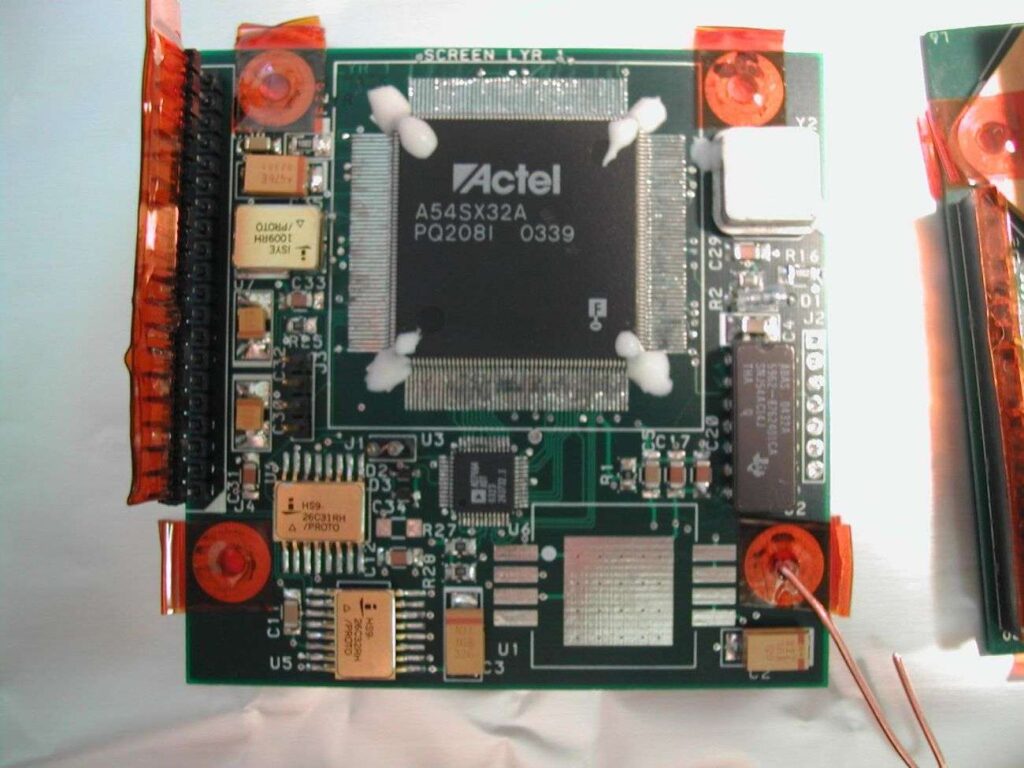
Industrial electronics are the lifeblood of modern manufacturing and automation. From power supplies and drives to servo motors and circuit boards, these components keep production lines running smoothly.
But like any critical system, they face their share of challenges. Understanding and addressing these issues early can help minimize downtime and reduce costly repairs.
Here’s a closer look at some of the most common maintenance challenges and how to manage them effectively.
1. Environmental Contaminants
Dust, moisture, and heat are some of the most common and damaging threats to industrial electronics. These elements can cause a range of issues—from blocked airflow and overheating to corrosion and electrical shorts.
Solution: Schedule regular cleanings of your electronic equipment. Use non-static generating compressed air and ensure your plant environment is well-ventilated. Keep backup equipment stored in dry, clean conditions to avoid damage before use.
2. Loose Connections and Vibration Damage
Vibration is a constant in industrial settings and one of the leading causes of loose connections. Left unchecked, this can lead to arcing, erratic behavior, and premature failure of equipment like variable frequency drives (VFDs), circuit boards, and encoders.
Solution: Incorporate a preventive maintenance (PM) program that includes checking and securing all wiring connections. Look for signs of wear on connectors and components, and use thermal imaging tools to detect heat issues from poor connections.
3. Power Problems
Power supply issues range from underpowered units to surges and reversed polarity. These problems can cause shutdowns or more severe damage to sensitive electronics.
Solution: Use surge protectors and uninterruptible power supplies (UPS) where applicable. Ensure your power supply matches the load requirements of your system, and inspect for any loose wiring or polarity mismatches during installation or repair.
4. Component Aging and Failure
Capacitors, resistors, and other discrete components degrade over time. You may not notice a slow decline in performance until it results in full equipment failure.
Solution: Check for signs of bulging or leaking capacitors, corrosion, or burnt components. If possible, replace aging parts before they fail. Using a repair service with diagnostic tools can help catch issues early and save costs.
5. Misalignment and Mechanical Wear
Motors and encoders suffer when improperly aligned or subjected to excessive mechanical stress. Common symptoms include increased noise, vibration, and output irregularities.
Solution: Regularly inspect equipment alignment and watch for warning signs like unusual noises. Proper tuning and lubrication are also essential for extending equipment lifespan.
Stay Ahead of Failures with Expert Help from ACS
Proactive maintenance goes a long way, but even the best-kept systems may run into trouble. That’s where expert repair services come in. At ACS Industrial Services, we provide fast, thorough evaluations and quality repairs for all types of industrial electronics.
Call ACS Industrial for Repairs and Service for Your Industrial Electronics!
Knowing how to keep industrial electronics in operation can be tough, but you don’t have to do it alone. At ACS Industrial Services, we specialize in preventative maintenance and repair services for industrial electronic equipment.
With over 20 years of experience, ACS is a leading industrial repair service provider when things break. We repair many different components of machinery across various makes and models. We provide a rapid turnaround time. Most repairs are back in your hands within 7-15 business days, with our Rush Repair Service typically shipping in just 3-5 business days.
Contact us for a FREE evaluation and a no-obligation quote, or call (800) 605-6419.