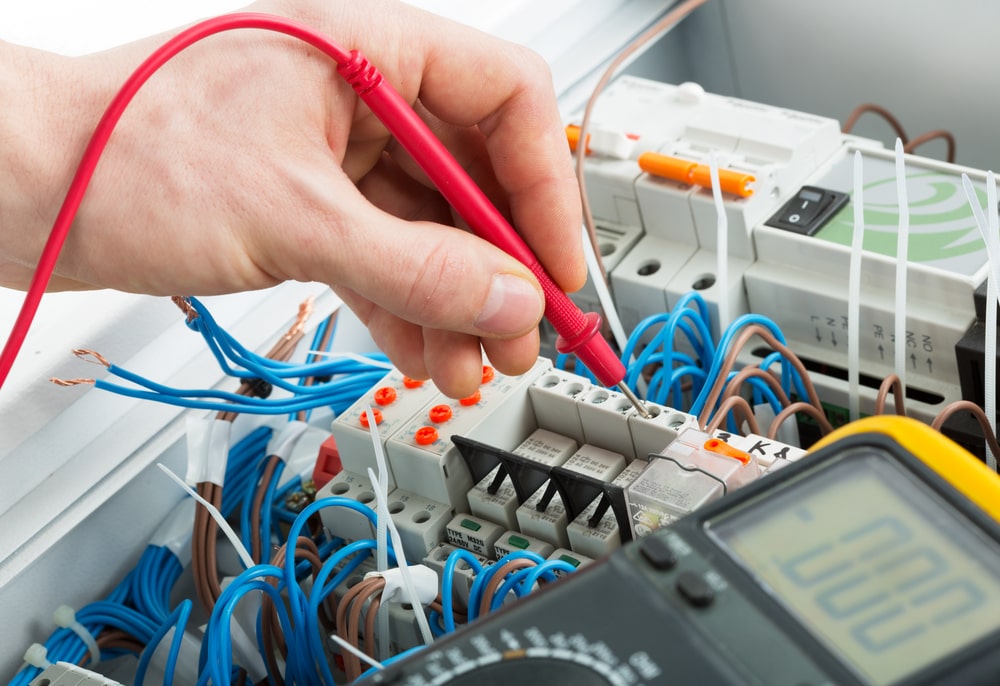
Industrial electronics are essential for keeping automated systems, machinery, and production lines running smoothly. Over time, these components can fail due to wear, electrical surges, or environmental factors. When this happens, businesses must decide whether to repair the faulty equipment or replace it with a new unit. Making the right choice depends on cost, availability, and long-term reliability.
Understanding Industrial Electronic Repair
Repairing industrial electronics involves diagnosing faults, replacing damaged parts, and restoring functionality. Skilled technicians use specialized tools to troubleshoot and fix circuit boards, power supplies, and control modules. Repairs are typically done by third-party service providers who specialize in industrial electronics.
When Repair Is the Better Option
In many cases, repairing existing equipment is the more practical choice. If a component has only minor damage or is still fundamentally sound, repairs can fully restore functionality at a fraction of replacement cost. Older models often have proven reliability, simpler designs that are easier to fix, and established compatibility with your existing systems.
If repair costs are less than 50% of the price of a new unit, fixing the current equipment is typically the smarter investment. Additionally, with potential supply chain delays and long lead times for new equipment, a well-executed repair can get your system back online much faster, minimizing costly downtime.
Cost Considerations for Repair and Replacement
Cost is a major factor in deciding between repair and replacement. Repairing electronics is often cheaper upfront, but frequent failures may increase long-term expenses. Replacement requires a higher initial investment but can reduce maintenance costs and downtime in the future.
Businesses should also consider indirect costs, such as lost production time and installation labor. A cost-benefit analysis helps determine which option provides the best value over time.
Evaluating Downtime and System Disruption
Downtime caused by equipment failure can lead to lost revenue and decreased productivity. Repairs are often faster than sourcing and installing a new unit, especially if spare parts are available. However, if repaired equipment fails again shortly after servicing, downtime could increase.
Replacement eliminates the risk of recurring failures, but requires additional time for procurement and set up. You’ll need to plan ahead and maintain backup components to minimize disruption.
Environmental and Sustainability Factors
Repairing industrial electronics supports sustainability by reducing electronic waste. Manufacturing new equipment consumes raw materials and energy, contributing to environmental impact. Many businesses prioritize eco-friendly practices and seek to extend the lifespan of existing equipment.
However, if a system is highly inefficient or contains hazardous materials, replacement with energy-efficient alternatives may be the more responsible choice.
Making the Best Choice
Choosing between repair and replacement requires a careful assessment of cost, downtime, performance, and environmental impact.
Regular maintenance and condition monitoring can help prevent unexpected failures and extend equipment lifespan. Consulting with industry experts or repair specialists like ACS Industrial can provide insights into the best course of action.
Each situation is unique, so businesses must weigh the benefits and risks before making a final decision.
Call ACS Industrial and Make the Smart Choice for Your Industrial Electronics
Knowing how to keep industrial electronic equipment in good working order can be tough, but you don’t have to do it alone. At ACS Industrial Services, we specialize in preventative maintenance and repair services for industrial equipment.
With over 20 years of experience, ACS is a leading industrial repair service provider when things break. We repair many different components of machinery across various makes and models. We provide a rapid turnaround time. Most repairs are back in your hands within 7-15 business days, with our Rush Repair Service typically shipping in just 3-5 business days.
Contact us for a FREE evaluation and a no-obligation quote, or call (800) 605-6419.