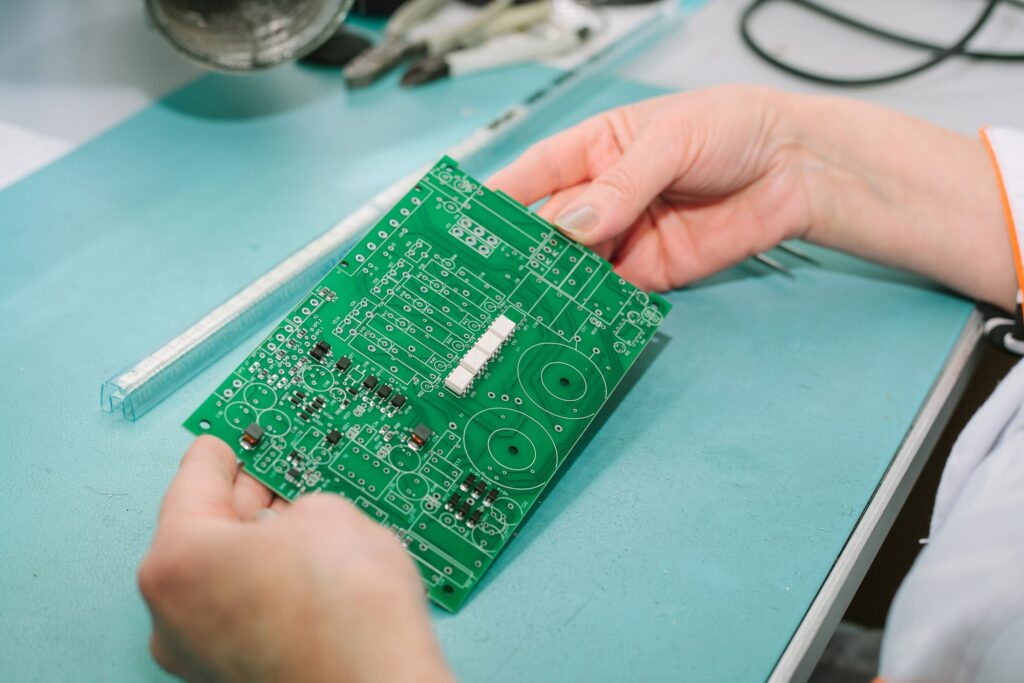
Industrial control boards are like the brains of factory equipment. They run assembly lines, robots, and other machines in factories. When these boards break down, work stops. This can cost companies a lot of money.
These boards can have many problems. Sometimes they lose power. Other times they stop talking to other parts of the system. They can also get damaged by heat, dust, or vibration in factories. Before you try to fix one yourself, you should understand what you’re dealing with.
Understanding Industrial Control Boards
Industrial control boards are tougher than the circuit boards in your home electronics. They’re built to handle rough conditions like shaking, extreme temperatures, and running 24/7. These boards often have special coatings and stronger parts.
Most industrial boards connect to many different things at once – power supplies, motors, sensors, and communication networks. This makes them harder to fix than home electronics. These boards also use special connectors made just for factory equipment.
When Professional Repair Makes Sense
Safety is very important in factories. Control boards often connect to high-voltage systems that run heavy machines. Bad repairs can cause fires, make machines move unexpectedly, or disable safety features. These risks can lead to worker injuries, not just broken equipment.
Today’s industrial control systems often use special technology and custom programming. Professional repair people have access to manufacturer instructions, testing methods, and original parts. They also understand how fixing one board might affect other parts of the system.
Many equipment warranties require repairs by OEM technicians. Using non-OEM repairs or aftermarket parts while the item is still under warranty can void warranties for expensive systems. Always check warranty rules before trying repairs yourself.
Essential Skills for In-House Repair
Basic electrical testing is a must-have skill. Maintenance workers should know how to safely measure voltage, check connections, and spot failed components. Understanding how to read electrical diagrams helps find problems.
Industrial boards require special handling techniques. They often have thicker metal traces, extra mounting hardware, and protective coatings. Proper cleaning is essential to ensure good connections in dirty factory environments.
Good record-keeping is crucial. Anyone doing repairs should write down what was wrong, how they fixed it, and what parts they used. This information helps with future problems and planning maintenance.
Developing a Balanced Approach
Many factories use a tiered approach. Maintenance staff handle simple fixes like replacing connectors or fuses. They send more complex repairs to professional technicians. This approach minimizes downtime while managing risks.
Consider keeping spare boards for critical systems. While this costs money upfront, having replacement boards ready allows quick system recovery while damaged boards get proper repair without rushing.
Training pays off. Even if your team can’t do complex repairs, basic electronics training helps them identify problems correctly, talk effectively with repair services, and avoid making problems worse.
Making the Final Decision
Think about your specific needs. Continuous production factories where downtime costs thousands per minute might need more in-house repair capability. Smaller operations might do better with service contracts that guarantee quick response times.
The complexity of your systems matters too. Older, simpler control boards are easier to repair than newer boards with tiny components and multiple layers.
A smart approach balances urgent needs against long-term reliability. In-house repairs can fix immediate problems while professional services ensure lasting solutions. By understanding what both approaches can and cannot do, you can develop a maintenance plan that keeps your industrial systems running reliably.
Call ACS Industrial for Repairs and Service for Your Control Boards!
Knowing how to keep your industrial electronic equipment running can be tough, but you don’t have to do it alone. At ACS Industrial Services, we specialize in preventative maintenance and repair services for industrial electronic equipment.
With over 20 years of experience, ACS is a leading industrial repair service provider when things break. We repair many different components of machinery across various makes and models. We provide a rapid turnaround time. Most repairs are back in your hands within 7-15 business days, with our Rush Repair Service typically shipping in just 3-5 business days.
Contact us for a FREE evaluation and a no-obligation quote, or call (800) 605-6419.